Obecnie na świecie istnieją trzy rodzaje płaskiego szkła: płaskie ciągnienie, metoda float i kalandrowanie. Szkło float, które obecnie stanowi ponad 90% całkowitej produkcji szkła, jest podstawowym materiałem budowlanym w światowym szkle architektonicznym. Proces produkcji szkła float został zapoczątkowany w 1952 r. i wyznaczył światowy standard produkcji wysokiej jakości szkła. Proces produkcji szkła float obejmuje pięć głównych etapów:
● składniki
● topienie
● formowanie i powlekanie
● wyżarzanie
● cięcie i pakowanie
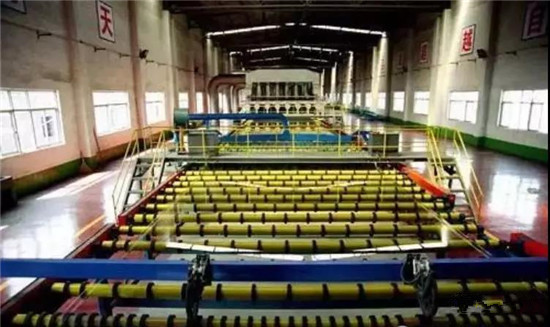
Składniki
Dozowanie jest pierwszym etapem, który przygotowuje surowce do topienia. Surowce obejmują piasek, dolomit, wapień, sodę kalcynowaną i mirabilit, które są transportowane ciężarówkami lub pociągiem. Surowce te są przechowywane w pomieszczeniu dozującym. W pomieszczeniu materiałowym znajdują się silosy, leje, przenośniki taśmowe, zsuwnie, odpylacze i niezbędne systemy sterowania, które kontrolują transport surowców i mieszanie materiałów wsadowych. Od momentu dostarczenia surowców do pomieszczenia materiałowego, są one stale w ruchu.
Wewnątrz pomieszczenia dozującego długi płaski przenośnik taśmowy nieprzerwanie transportuje surowce z silosów różnych surowców do przenośnika kubełkowego warstwa po warstwie, a następnie przesyła je do urządzenia ważącego w celu sprawdzenia ich łącznej masy. Do tych składników dodawane są fragmenty szkła pochodzące z recyklingu lub zwroty z linii produkcyjnej. Każda partia zawiera około 10-30% stłuczonego szkła. Suche materiały są dodawane do mieszalnika i mieszane z partią. Wymieszana partia jest wysyłana z pomieszczenia dozującego do silosu głowicy pieca w celu przechowywania za pomocą przenośnika taśmowego, a następnie dodawana do pieca w kontrolowanym tempie przez podajnik.

Typowy skład szkła
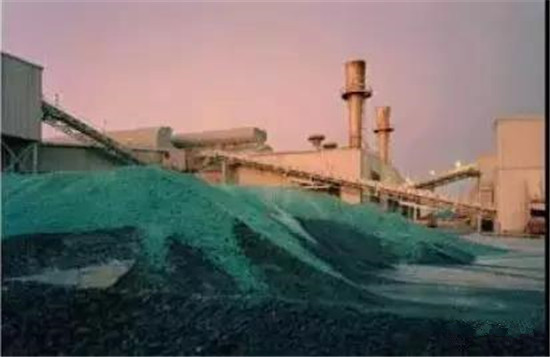
Skład stłuczki
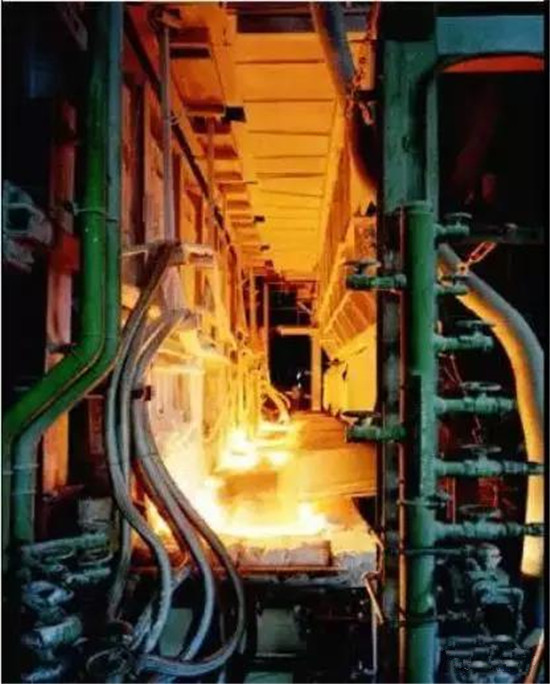
Podawanie zmieszanych surowców do wlotu pieca o temperaturze do 1650 stopni za pomocą zasobnika
Topienie
Typowy piec to poprzeczny piec płomieniowy z sześcioma regeneratorami, o szerokości około 25 metrów i szerokości 62 metrów, o dziennej wydajności produkcyjnej 500 ton. Głównymi częściami pieca są basen topielny/klarownik, basen roboczy, regenerator i mały piec. Jak pokazano na rysunku 4, jest on wykonany ze specjalnych materiałów ogniotrwałych i ma stalową konstrukcję na zewnętrznej ramie. Wsad jest wysyłany do basenu topielnego pieca przez podajnik, a basen topielny jest podgrzewany do 1650 ℃ przez pistolet natryskowy na gaz ziemny.
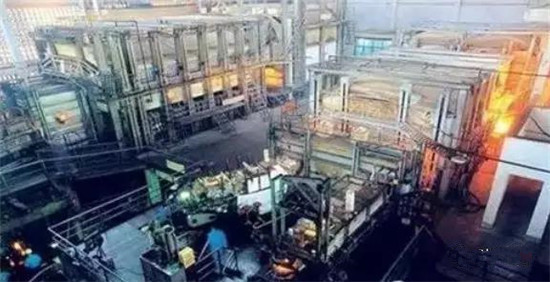
Roztopione szkło przepływa z basenu do obszaru szyjki przez klarownik i jest równomiernie mieszane. Następnie przepływa do części roboczej i powoli schładza się do około 1100 stopni, aby osiągnąć odpowiednią lepkość przed dotarciem do kąpieli cynowej.
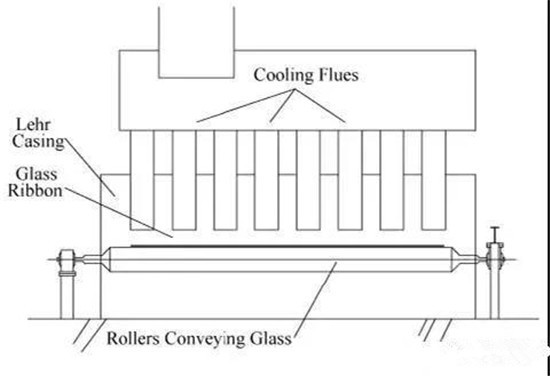
Formowanie i powlekanie
Proces formowania klarownego szkła ciekłego w płytę szklaną jest procesem mechanicznej manipulacji zgodnie z naturalną tendencją materiału, a naturalna grubość tego materiału wynosi 6,88 mm. Szkło ciekłe wypływa z pieca przez obszar kanału, a jego przepływ jest kontrolowany przez regulowane drzwi zwane tłokiem, które są około ± 0,15 mm głęboko w szkle ciekłym. Pływa na stopionej cynie - stąd nazwa szkło float. Szkło i cyna nie reagują ze sobą i można je rozdzielić; Ich wzajemny opór w formie molekularnej sprawia, że szkło jest gładsze.
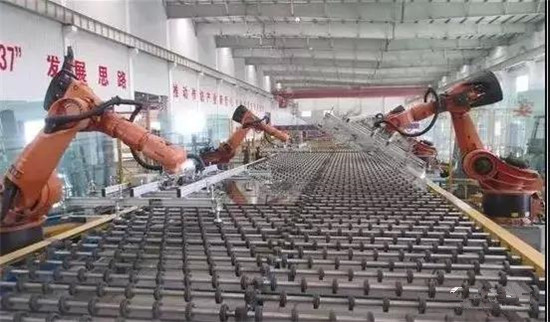
Kąpiel jest jednostką uszczelnioną w kontrolowanej atmosferze azotu i wodoru. Obejmuje stal nośną, górną i dolną powłokę, materiały ogniotrwałe, cynę i elementy grzewcze, atmosferę redukującą, czujniki temperatury, komputerowy system sterowania procesem, około 8 metrów szerokości i 60 metrów długości, a prędkość linii produkcyjnej może osiągnąć 25 metrów / minutę. Kąpiel cynowa zawiera prawie 200 ton czystej cyny, ze średnią temperaturą 800 ℃. Kiedy szkło tworzy cienką warstwę na końcu wlotu kąpieli cynowej, nazywa się to płytą szklaną, a seria regulowanych ściągaczy krawędzi działa po obu stronach. Operator używa programu sterującego do ustawienia prędkości pieca do wyżarzania i maszyny do ciągnienia krawędzi. Grubość płyty szklanej może wynosić od 0,55 do 25 mm. Górny element grzejny przegrody służy do kontrolowania temperatury szkła. Ponieważ płyta szklana ciągle przepływa przez kąpiel cynową, temperatura płyty szklanej będzie stopniowo spadać, dzięki czemu szkło będzie płaskie i równoległe. W tym momencie acuracoat może być używany ® do galwanizacji on-line folii odblaskowej, folii niskoemisyjnej, folii przeciwsłonecznej, folii fotowoltaicznej i folii samoczyszczącej na sprzęcie pirolizy CVD. W tym momencie szkło jest gotowe do schłodzenia.
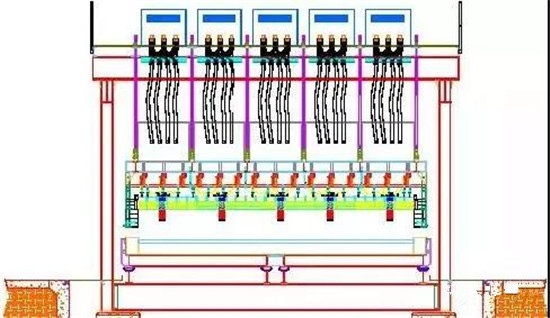
Przekrój wanny
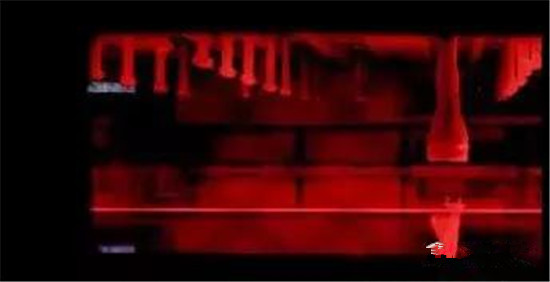
Szkło rozprowadza się cienką warstwą na stopionej puszce, oddziela od puszki i formuje w talerz
Zawieszony element grzewczy zapewnia dopływ ciepła, a szerokość i grubość szkła są kontrolowane przez prędkość i kąt nachylenia krawędzi.
Wyżarzanie
Gdy uformowane szkło opuszcza kąpiel cynową, jego temperatura wynosi 600 ℃. Jeśli płyta szklana jest chłodzona w atmosferze, powierzchnia szkła będzie się schładzać szybciej niż wnętrze szkła, co spowoduje poważne ściśnięcie powierzchni i szkodliwe naprężenie wewnętrzne płyty szklanej.
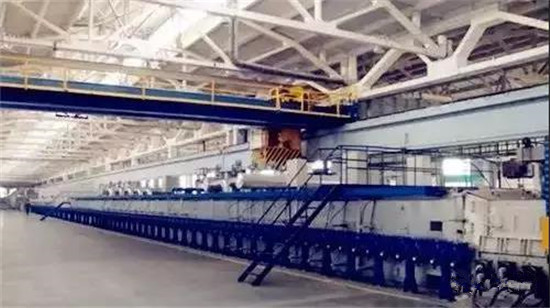
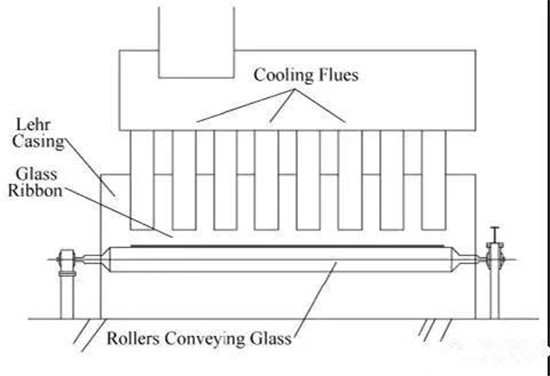
Sekcja pieca do wyżarzania
Proces nagrzewania szkła przed i po formowaniu jest również procesem formowania naprężeń wewnętrznych. Dlatego konieczne jest kontrolowanie ciepła, aby stopniowo obniżać temperaturę szkła do temperatury otoczenia, czyli wyżarzanie. W rzeczywistości wyżarzanie odbywa się w piecu do wyżarzania z wstępnie ustawionym gradientem temperatury (patrz rysunek 7) o szerokości około 6 metrów i długości 120 metrów. Piec do wyżarzania obejmuje elektrycznie sterowane elementy grzewcze i wentylatory, aby utrzymać stabilny rozkład temperatury poprzecznej płyt szklanych.
W wyniku procesu odprężania szkło zostaje ostrożnie schłodzone do temperatury pokojowej, bez chwilowych naprężeń lub naprężeń.
Cięcie i pakowanie
Płyty szklane schłodzone w piecu do wyżarzania są transportowane do strefy cięcia przez stół rolkowy połączony z układem napędowym pieca do wyżarzania. Szkło przechodzi przez system kontroli on-line w celu wyeliminowania wszelkich wad i jest cięte diamentową tarczą tnącą w celu usunięcia krawędzi szkła (materiał krawędzi jest poddawany recyklingowi jako stłuczone szkło). Następnie jest cięte na rozmiar wymagany przez klienta. Powierzchnia szkła jest posypywana proszkowym medium, dzięki czemu płyty szklane można układać w stosy i przechowywać, aby uniknąć sklejania się lub zarysowania. Następnie nieskazitelne płyty szklane są dzielone na stosy w celu pakowania za pomocą maszyn ręcznych lub automatycznych i przenoszone do magazynu w celu przechowywania lub wysyłki do klientów.
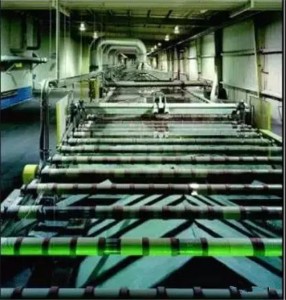
Po opuszczeniu pieca do wyżarzania, płyta szklana jest w pełni formowana i przenoszona do strefy chłodzenia w celu dalszego obniżania temperatury